TL;DR – Key Takeaways
- Predictive analytics monitors equipment health using sensor data to anticipate failures, enabling timely maintenance and avoiding costly unplanned shutdowns.
- Accurate demand forecasting optimizes inventory, enhances supplier relationships, and improves on-time, in-full delivery, reducing waste and avoiding stockouts.
- Price optimization tools analyze cost, competitor, and customer data to set ideal pricing strategies.
- Analytics enables informed design decisions by tracking customer feedback, IoT data, and warranty claims, leading to higher product quality, better market fit, and reduced launch risks.
- Smart manufacturing technologies like AI and robotics automate repetitive or hazardous tasks.
- Real-time data from sensors and cameras ensures product consistency. Boeing’s predictive analytics in aviation parallels these principles by preventing defects through advanced monitoring and anomaly detection.
Managing the sheer volume of data generated across operations can feel overwhelming in manufacturing. You're likely dealing with scattered information, making gaining real insights that drive efficiency tough. Decision-making becomes slow and inaccurate without a clear strategy for harnessing this data. This is where manufacturing analytics steps in. Centralizing and analyzing key data points allows you to streamline processes and make informed decisions that boost productivity.
According to Market Research Future (MRFR), the manufacturing analytics market is poised for substantial growth, with an expected CAGR of 15.70% over the forecast period. By 2032, it’s projected to reach USD 19.1 billion, driven by manufacturers' need to leverage data-driven strategies to maintain a competitive edge.
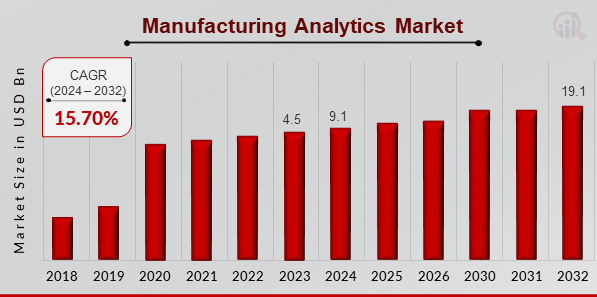
In this article, we'll explore the top manufacturing analytics use cases and show how this rapidly growing market can help turn your data into a powerful asset for growth. Let’s begin with the basics and discuss what manufacturing analytics is.
What is Manufacturing Analytics and How Does it Work
Manufacturing analytics is the process of capturing, cleansing, and analyzing data from machines, processes, and even human input across all stages of production. This structured and unstructured data is collected through software or manually, creating a comprehensive view of the entire manufacturing process. By transforming raw data into actionable insights, manufacturing analytics helps manufacturers monitor production in real-time, spot inefficiencies, and uncover opportunities for improvement.
The purpose of manufacturing analytics goes beyond simple data collection; it enables manufacturers to predict future use, anticipate maintenance needs, and prevent potential failures before they impact production. This predictive capability enhances decision-making, allowing manufacturers to improve efficiency, maintain high product quality, and reduce waste. Ultimately, manufacturing analytics empowers organizations to operate more strategically, making data-driven decisions that contribute to streamlined operations and a stronger competitive position. Let's break this down step-by-step.
Manufacturing analytics involves several key actions:
- Data Collection: Machines, sensors, and other equipment in a factory generate large amounts of data every second. This can include information like machine performance, production speed, and product quality.
- Data Analysis: Once data is collected, advanced tools process and analyze data for insights.. For instance, if a machine's temperature suddenly spikes, the system alerts you to potential issues before they cause breakdowns.
- Decision-Making: The insights drawn from analytics help manufacturers make smarter decisions. For example, if one production line is more efficient than another, you can use that data to improve the slower line.
Why Is It Important?
Understanding the significance of manufacturing analytics is vital for success. It empowers businesses to enhance productivity, minimize waste, and ensure quality. Manufacturing analytics is crucial because it:
- Reduces Downtime: By predicting when machines need maintenance, you can prevent unexpected failures and keep production moving smoothly.
- Improves Product Quality: Analytics can detect small issues in the production process before they turn into bigger problems. This ensures that the final products meet the highest quality standards.
- Increases Efficiency: By tracking how every machine and worker performs, you can identify bottlenecks and areas for improvement, leading to faster production times.
For example, imagine you run a factory that makes smartphones. Each phone goes through several stages—assembly, testing, packaging, and shipping. Let’s say you notice that one assembly line finishes faster than the others. Manufacturing analytics shows you that certain machines on the slower lines are underperforming. After analyzing the data, you find that these machines are due for maintenance. Addressing this can bring all lines up to speed, reducing delays and improving overall output.
Now that we understand how manufacturing analytics works, let’s explore its top applications.
9 Must-Know Use Cases for Manufacturing Analytics
A Gartner study predicts that by 2025, 70% of manufacturing companies will shift from analytics to small and wide data. This change will help manufacturers use data more effectively. It will make their operations smoother and improve decision-making.
This section will look at the top manufacturing analytics use cases. These examples will show how organizations can make the most of their data.
1. Predictive Analytics
Predictive analytics helps manufacturers look at current data to predict and prevent problems before they happen. This method keeps operations running smoothly and ensures everything works well. By using predictive analytics, companies can find ways to solve issues early, which improves productivity and saves money.
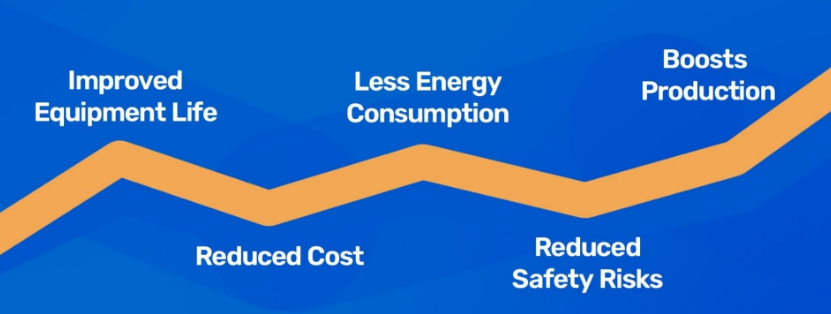
Predictive analytics is very useful for predicting equipment failures and planning maintenance. This helps manufacturers reduce unexpected breakdowns.
Suppose a factory uses sensors to monitor its assembly machines. These sensors keep track of things like temperature and vibrations. If the sensors detect a machine getting too hot, they can alert the workers before it stops working. This way, the factory can fix the machine before it causes production delays.
Types of Preventive Maintenance
There are two main types of preventive maintenance: time-based and usage-based.
- Time-Based Maintenance: This type involves checking machines at regular intervals. For example, a factory might inspect its paint sprayer every three months. This routine check helps catch small problems before they lead to bigger ones.
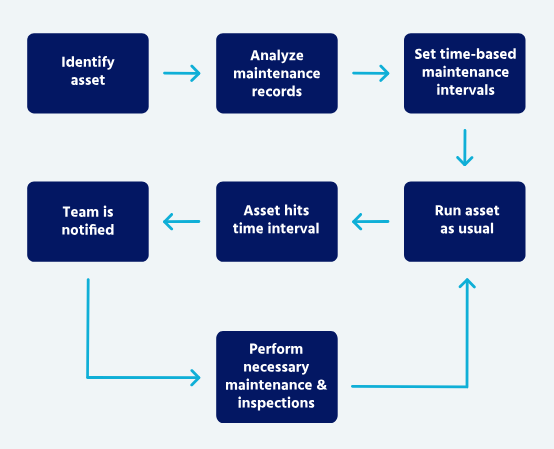
- Usage-Based Maintenance: This method focuses on how often machines are used. For instance, if a packaging machine has been running for a certain number of hours, the factory schedules a checkup. This way, the machine only gets serviced when needed, which helps keep everything running smoothly.
Within user-based maintenance, three key approaches—FBM (Fixed-Based Maintenance), UBM (Usage-Based Maintenance), and CBM (Condition-Based Maintenance)—help optimize equipment performance based on specific criteria.
- FBM (Fixed-Based Maintenance): This approach schedules maintenance at set intervals regardless of equipment usage. For instance, a machine may receive servicing every six months, whether heavily used or barely operated. FBM is straightforward but may result in over-maintenance or missed issues between intervals.
- UBM (Usage-Based Maintenance): UBM is tailored to the actual usage of equipment. Maintenance occurs after a set number of operating hours or cycles, making it ideal for machinery with consistent use patterns. For example, servicing might be scheduled every 500 hours, ensuring maintenance aligns with wear and tear.
- CBM (Condition-Based Maintenance): CBM monitors the real-time condition of equipment through sensors or IoT data to determine when maintenance is needed. This approach reduces unnecessary servicing by responding directly to wear or malfunction indicators, improving efficiency, and preventing unexpected breakdowns.
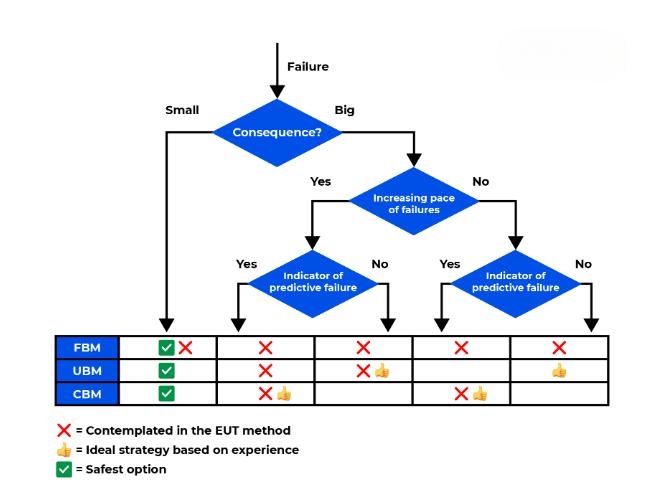
The biggest benefit of using predictive analytics for maintenance is better planning. When manufacturers know when problems might arise, they can schedule repairs during slower times.
For example, Ford, one of the world's leading automobile manufacturers, expertly utilizes predictive maintenance through advanced manufacturing analytics. Ford can continuously monitor equipment performance by integrating specialized sensors called miniterms into their machinery. These sensors promptly alert engineers to any drops in machine speed, allowing for quick maintenance before issues escalate. Since implementing this system, Ford has saved over €1 million in downtime costs.
Demand Forecasting and Inventory Management
Demand forecasting is an essential process that analyzes data to predict future product needs. It is closely tied to inventory management and relies heavily on supply chain data. Understanding this connection helps manufacturers make informed decisions.
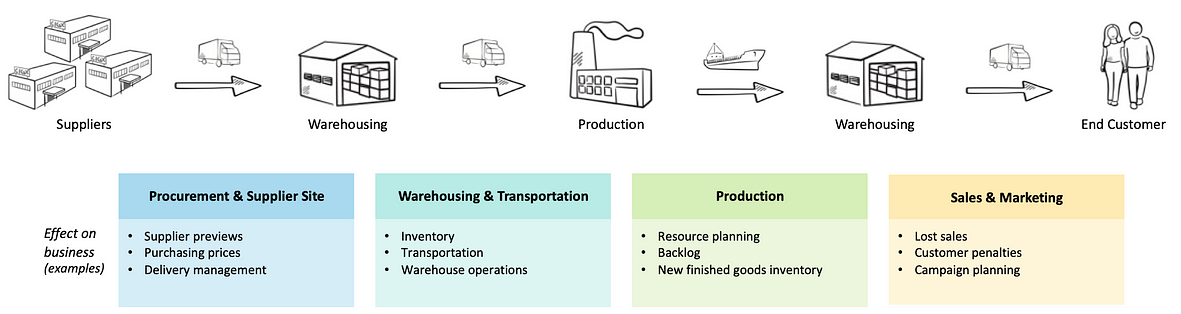
Accurate demand forecasting offers several benefits for manufacturers, including:
- Better Inventory Control: This minimizes the need to store excess products that may not sell. For instance, if a toy manufacturer can accurately predict demand for a new action figure, they can adjust their production accordingly, avoiding surplus stock.
- Improved Supplier Relationships: Effective demand forecasting enhances relationships between suppliers and manufacturers. With accurate forecasts, both parties can better manage inventory levels and streamline the supply process. For example, if a manufacturer knows they will need a specific quantity of materials in advance, they can communicate this to their suppliers, ensuring timely deliveries.
- Improved OTIF (On-time in-Full): Excellent demand forecasting helps manufacturers maintain great OTIF.
When conducting demand forecasting and managing inventory, manufacturers must consider various factors, such as:
- Economic Conditions: Changes in the economy can affect consumer demand.
- Market Trends: Keeping an eye on industry trends helps make informed predictions.
- Raw Material Availability: Ensuring that materials are available for production is crucial.
For example, Unilever’s use of AI for demand forecasting and inventory management offers a strong example of how manufacturing analytics can streamline operations. They leverage AI-driven tools to predict local demand and optimize inventory in real-time, reducing waste and ensuring products are available where needed. By predicting demand more accurately, Unilever maintains better stock levels, enhancing efficiency and sustainability across its supply chain. Predictive analytics aligns with key manufacturing analytics applications, directly improving inventory management and customer satisfaction.
Price Optimization
Setting the right price for a product involves considering many factors influencing its final cost. Everything from the initial price of raw materials to distribution costs contributes to this figure. But what happens when customers find the price either too high or too low?
Price optimization is determining the best possible price for manufacturers and customers—finding a price that is neither too high nor too low.
For example, in the automotive industry, a car manufacturer must consider:
- Raw Material Costs: Steel, plastics, and electronics prices directly impact production costs.
- Labor Expenses: Wages and benefits for workers contribute to overall production costs.
- Distribution Costs: Shipping and logistics costs are critical for getting the product to dealerships.
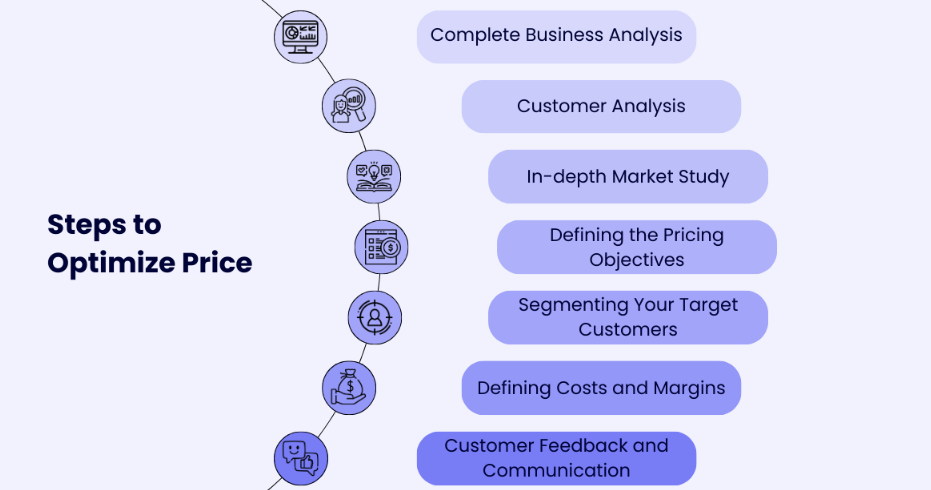
Modern price optimization solutions can significantly enhance profitability. These tools aggregate and analyze pricing and cost data from internal sources and competitors to suggest optimized price points. For instance, if a manufacturer analyzes market data and finds that similar vehicles are priced lower, they can adjust their pricing strategy accordingly.
Price optimization is essential in today's highly competitive market, where customer needs can change rapidly. It evolves into a continuous process that requires constant monitoring and adjustment.
Key aspects of price optimization include:
- Market Analysis: Regularly assessing competitor pricing and market trends to stay competitive.
- Customer Feedback: Gathering insights from customers to understand their price sensitivity and perceived value.
- Dynamic Pricing Strategies: Implementing flexible pricing models that can adapt to changes in demand and supply.
By focusing on these elements, manufacturers can ensure that their pricing strategies remain effective, maximizing both sales and customer satisfaction.
For example, General Electric’s pricing strategy shows how they use value-based pricing—setting prices based on the value products bring to customers. This use case can enhance price optimization in manufacturing analytics by analyzing customer needs, market conditions, and usage data. By understanding these variables, manufacturers can refine pricing to match customer value, especially for high-value equipment like jet engines or medical devices, maximizing profitability while remaining competitive.
Product Development
Data analytics has opened up significant opportunities for manufacturing companies in product development. Manufacturers leverage analytics to understand their customers better, meet demand, and fulfill their needs. By analyzing this data, companies can develop or improve new products.
Using analytics for product development allows manufacturers to create products that offer greater customer value while reducing the risks associated with launching new items.
Key benefits of utilizing analytics in this process include:
- Enhanced Customer Insights: Manufacturers can better understand what customers want by analyzing purchasing patterns and preferences. For example, an automotive manufacturer may use data to determine the most desired features in electric vehicles.
- Informed Decision-Making: IoT analytics can provide real-time insights into critical product parameters, enabling manufacturers to make informed adjustments that enhance product design. For instance, tracking wear and tear through IoT-enabled sensors highlights areas of improvement, helping engineers refine materials and components for greater durability and performance. Additionally, analyzing warranty and service data can reveal common issues, allowing manufacturers to address design flaws early on and improve overall product reliability. By integrating manufacturing analytics across these stages, companies can proactively refine designs, meet customer expectations, and boost product quality.
Customer feedback plays a crucial role in the product development process. Manufacturers can contribute valuable insights during the idea generation stage by collecting and analyzing this feedback.
This collaborative approach leads to:
- Improved Product Design: Feedback helps identify gaps in the market, allowing manufacturers to create products that better serve customer needs. For instance, if customers desire enhanced safety features, manufacturers can incorporate them into their designs.
- Higher Profitability: Manufacturers increase the likelihood of successful market introductions by developing products that align closely with customer expectations. A well-received product can lead to greater sales and customer loyalty.
For example, Foxconn’s entry into the EV market emphasizes rapid, data-driven product development through partnerships and technology integration. This approach aligns closely with manufacturing analytics in product development, where insights help optimize design, streamline production, and effectively meet market needs. Foxconn’s strategy showcases how manufacturing analytics can boost innovation and speed in complex industries like EVs.
Robotization and Automation
The smart manufacturing market is valued at USD 106.75 billion in 2023 and is projected to grow to USD 359.3 billion by 2031, with a compound annual growth rate (CAGR) of 16.56% during the forecast period from 2024 to 2031. Technologies such as robotics, artificial intelligence (AI), and machine learning are at the forefront of this transformation, enabling automation and reducing the need for manual labor while boosting production efficiency.
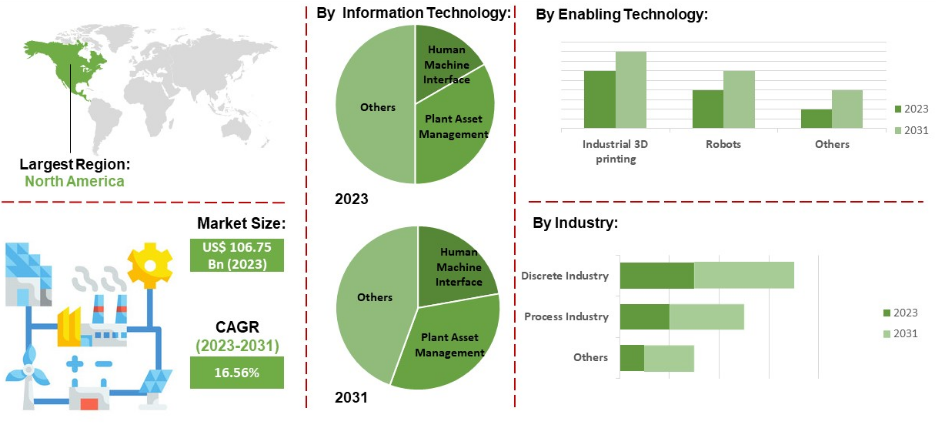
For instance, robots can perform repetitive tasks with greater accuracy and speed than humans. Meanwhile, AI and machine learning analyze vast amounts of data to optimize manufacturing processes and identify areas for improvement. This shift is driven by several factors, including:
- Rising Adoption of Industry 4.0: Companies increasingly embrace smart manufacturing practices to enhance efficiency.
- Demand for Time and Cost-Saving Software: Manufacturers seek solutions that streamline operations and reduce expenses.
- Complex Supply Chains: As supply chains grow more intricate, smart manufacturing technologies provide essential support.
- Emphasis on Regulatory Compliance: Businesses prioritize compliance with industry regulations, further fueling the need for automation.
Robots are revolutionizing the manufacturing landscape. Today, it is common for companies to use robots for routine tasks and jobs that may be hazardous for human workers.
For example, Siemens Electronics Works in Amberg is a leader in smart manufacturing. It produces advanced PLC systems like the S7-300 and S7-1500, ET200SP I/O systems and HMI panels. With an impressive 350 production changeovers daily and a portfolio of 1,200 products, the factory processes 17 million components each year. By leveraging data analysis, Siemens showcases how real-time insights enhance efficiency and innovation, making it a prime example of cutting-edge manufacturing technology.
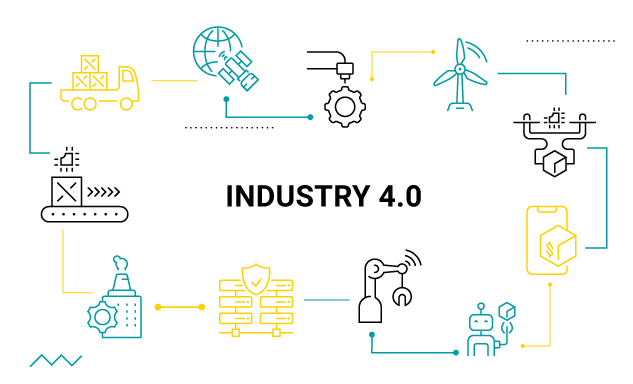
AI-powered robots play a crucial role in enhancing product quality. Each year, new and improved robot models are introduced to production floors, transforming manufacturing lines. These advanced robots are not only user-friendly but also more affordable for companies than ever before.
To maximize the benefits of smart manufacturing, organizations can:
- Identify Opportunities for Automation: Look for areas within the production process where automation can enhance efficiency.
- Use AI to Generate Instructions for Robotic Applications: Leverage AI capabilities to create precise instructions for robots, optimizing their performance.
By embracing these strategies, manufacturers can position themselves for success in the rapidly evolving smart manufacturing market.
Quality Control and Defect Detection
Ensuring high-quality standards in manufacturing is crucial. Small errors in production can lead to costly recalls or customer dissatisfaction. Quality control and defect detection using manufacturing analytics allow manufacturers to maintain consistent quality, prevent errors, and minimize waste.
Analytics systems can monitor production lines in real-time, identifying inconsistencies or standard deviations. For example, suppose a batch of products shows a higher-than-expected defect rate. In that case, manufacturing analytics can quickly pinpoint the exact stage where errors occur, such as faulty equipment or incorrect assembly techniques.
For example, The Boeing Flight Data Analytics news from Q2 2023 focuses on advancements in analytics to optimize aircraft performance, safety, and maintenance. While it addresses analytics applied to aerospace operations, its relevance to manufacturing analytics use cases in quality control and defect detection lies in similar data-driven principles. Boeing's approach to predictive maintenance, operational efficiency, and anomaly detection in aircraft performance parallels manufacturing analytics in monitoring quality and identifying defects for preventive action.
Advanced quality control analytics ensure each product meets precise specifications by analyzing data from sensors, cameras, and other tools throughout the process. Predictive algorithms also analyze historical quality data to identify patterns leading to defects, allowing teams to address problems preemptively.
Key factors include:
- Real-Time Monitoring: Immediate detection of production line issues, allowing for swift corrections.
- Root Cause Analysis: Identifying the underlying causes of recurring quality problems.
- Predictive Quality Management: Using historical data to prevent defects before they occur.
- Energy Management
Energy costs are a significant factor in manufacturing, impacting both expenses and environmental goals. Manufacturing analytics use cases in energy management enable companies to monitor, analyze, and optimize energy usage across production stages. By collecting real-time data from sensors and equipment, analytics tools help manufacturers identify inefficiencies, track usage patterns, and uncover savings opportunities.
For example, this E.ON case study showcases how the company utilizes advanced analytics for effective energy management. By transforming internal software into a scalable solution, E.ON enables business clients to track their energy consumption in real time. This approach supports customers in optimizing energy use, cutting costs, and meeting sustainability goals. Such use cases in manufacturing can benefit companies by improving efficiency, minimizing energy waste, and providing insights that help meet environmental objectives. This model demonstrates how data analytics drives sustainable energy practices in industrial settings.Key elements of energy management analytics include:
- Peak Load Management: Reducing energy use during high-cost periods.
- Process Optimization: Identifying and improving energy-intensive processes.
- Sustainability Tracking: Ensuring alignment with eco-friendly goals.
- Warehouse Management
Warehouse management in manufacturing analytics focuses on optimizing storage, handling, and product flow rather than just inventory counts. By analyzing data on storage conditions, product placement, and labor patterns, analytics helps manufacturers streamline warehouse layouts and minimize movement times.
For example, the Rolls-Royce Inventory Analysis report is highly relevant to manufacturing analytics in warehouse management. It outlines strategies for optimizing inventory by classifying items like "excess," "keep," and "partial" based on historical and forecasted usage. This approach aids in identifying surplus materials, reducing carrying costs, and ensuring item availability. By implementing data-driven classification, manufacturing facilities can streamline inventory management, minimize waste, and enhance supply chain reliability—key factors in efficient warehouse management for the manufacturing sector.Key aspects include:
- Space Utilization: Optimizing shelf placement and aisle layout to maximize capacity.
- Pick and Pack Efficiency: Enhancing order fulfillment with data-driven paths and organization.
- Labor Allocation: Distributing workforce based on peak periods and product movement trends.
Manufacturing analytics in warehouse management enable faster, more accurate order processing, reduced storage costs, and a better-organized warehouse.
- Achieving OEE (Overall Equipment Effectiveness)
Achieving high Overall Equipment Effectiveness (OEE) is essential in manufacturing, as it maximizes productivity by ensuring equipment operates at peak efficiency. Manufacturing analytics use cases in OEE provide real-time insights into equipment performance, identifying downtime causes and reducing production losses.
For example, Kordsa achieved high OEE by implementing Total Productive Maintenance (TPM) strategies focused on proactive maintenance and continuous improvement. They optimized machine performance through planned maintenance schedules, systematic problem-solving, and empowering employees to prevent breakdowns and defects. These initiatives enhanced equipment reliability and productivity, minimizing downtime and maximizing output. In manufacturing, such practices support OEE by aligning machine availability, performance, and quality, ultimately leading to efficient, high-yield production.Analytics enables manufacturers to monitor three critical OEE factors:
- Availability: Tracking equipment uptime to minimize unplanned stoppages.
- Performance: Measuring production speed against ideal rates for efficiency improvements.
- Quality: Monitoring output quality to reduce defect rates.
With analytics-driven OEE, manufacturers can optimize maintenance schedules, enhance productivity, and improve resource utilization, driving greater efficiency and profitability. These use cases highlight how manufacturing analytics drives results—let’s look at the specific benefits.
Key Benefits of Manufacturing Analytics
Manufacturing analytics offers a wealth of advantages that can transform your operations. By leveraging data effectively, businesses can enhance efficiency, improve quality, and achieve significant cost savings. Let's take a detailed look.
- Accelerated Time-to-Market
With data analytics, manufacturers can quickly detect emerging customer trends, enabling them to design, prototype, and produce new products faster. Staying ahead of market shifts allows manufacturers to be the first to offer innovative solutions—an advantage across all sectors.
- Smarter Prototyping and Testing
Analytics provides insights into customer preferences, allowing manufacturers to refine prototypes to align closely with market needs. By gathering data from initial testing, they can make data-driven improvements, ensuring products are optimized before reaching the market.
- Predictive Maintenance for Optimal Equipment Health
Through predictive maintenance, manufacturers can monitor machinery health in real-time, identifying wear and tear before it leads to costly breakdowns. This proactive approach maximizes uptime, extends equipment lifespan, and reduces unexpected production halts.
- Quality Control and Rapid Defect Detection
Data analytics enables manufacturers to identify defects early, ensuring products meet quality standards consistently. By addressing issues at the source, manufacturers reduce returns, improve customer satisfaction, and maintain high product reliability.
- Regulatory Compliance and Risk Management
Meeting regulatory standards is essential for manufacturing businesses. Analytics helps manufacturers stay compliant by proactively identifying and resolving potential issues and safeguarding against recalls, legal concerns, and compliance-related setbacks.
- Streamlined Supply Chain Management
With analytics, manufacturers can optimize inventory and logistics, ensuring materials are available when needed while avoiding costly overstock. This turns the supply chain into a precise, efficient operation, supporting reliable product availability.
- Optimal Workforce Allocation
Effective production requires the right workforce at the right time. Data analytics helps manufacturers predict staffing needs by analyzing past data and current trends, particularly during high-demand periods. This insight ensures balanced staffing levels without excessive labor costs.
- Long-Term Strategic Planning
Analytics empowers manufacturers to develop strategic plans that align with future revenue goals and evolving market demands. Manufacturers can create flexible, future-ready strategies that adapt to industry shifts by tracking and interpreting market trends.
- Profitability Gains Through Operational Efficiency
These data-driven production, quality control, staffing, and supply chain efficiency improvements significantly enhance profitability. Analytics-driven optimization leads to a healthier bottom line and supports sustained business growth.
While the benefits are clear, important factors should be considered before implementing this technology.
Key Factors to Evaluate Before Adopting Manufacturing Analytics
To effectively implement manufacturing analytics and maximize your results, consider these four essential questions:
- What specific areas or workflows do you aim to enhance with manufacturing analytics?
While data analytics can be applied across various departments, it’s crucial to pinpoint the specific areas you want to improve. Whether it’s product development, distribution, or quality control, clearly defining your goals will help you familiarize yourself with the technology and understand its potential benefits for your business. Starting with a focused approach also makes it more cost-effective to introduce analytics to select processes.
- Is your business infrastructure equipped to support data analytics?
Successfully gathering, storing, and analyzing data demands robust computing power, modern technology, and seamless connectivity between departments. Assess your current infrastructure to determine its readiness for this transition. Identify what adjustments are necessary for your tech stack and operational processes to accommodate the integration of manufacturing analytics.
- Are your employees aware of the benefits of manufacturing analytics?
For manufacturing analytics to reach its full potential, your team must recognize its value and understand how it can contribute to its implementation. Hosting training sessions and informative workshops can bridge this knowledge gap. You may also consider bringing in data analysts or external consultants to establish the analytics environment and help interpret the data effectively.
- How will you safeguard your data?
With manufacturing analytics relying on digital data storage, prioritizing cybersecurity is critical. Evaluate and choose reliable storage solutions that protect your enterprise data from cyber threats, detect suspicious activities, and prevent unauthorized access. Establishing a strong data security framework is essential to leveraging manufacturing analytics's benefits without compromising sensitive information.
Conclusion
Using manufacturing analytics helps companies work better and stay competitive. They can predict when machines need maintenance, forecast product demand, and manage inventory effectively. Businesses can take full advantage of data by ensuring their technology and employees are ready. The future of manufacturing relies on data-driven decisions.
Does it seem too complicated? - Here's how INSIA can help:
- Advanced-Data Analysis: INSIA’s Manufacturing Analytics tools provide tools to analyze large datasets, helping manufacturers uncover insights that drive efficiency and productivity.
- Seamless Integration: The platform easily integrates with existing systems, ensuring a smooth transition to data-driven processes.
- Real-Time Monitoring: Manufacturers can monitor operations in real-time, allowing for quick adjustments and proactive decision-making.
- User-Friendly Reporting: INSIA's no-code dashboarding makes it easy to visualize data and share insights across teams.
- Enhanced Collaboration: Teams can collaborate through shared reports and interactive comments, promoting informed decision-making.
- AI-Powered Insights: INSIA leverages AI to identify trends and suggest improvements, enhancing overall manufacturing performance.
- Robust Security: Data security measures protect sensitive information while enabling efficient data sharing.
Frequently Asked Questions (FAQs)
1. What Is Manufacturing Analytics and How Does It Help My Business?
Think of manufacturing analytics as a way to turn your factory data into actionable insights. By tracking everything from machine performance to product quality, you can make smarter decisions, spot inefficiencies, and keep your operations running smoothly. It helps you predict issues before they happen, reduce waste, and improve efficiency across the board.
2. How Can Predictive Maintenance Keep My Machines Running Smoothly?
Predictive maintenance is like having a crystal ball for your equipment. It uses real-time data—like temperature or vibrations—to let you know when something might break down. This means you can fix things before they fail, saving you from unexpected downtime and costly repairs. Your machines last longer, and you avoid production delays.
3. How Does Demand Forecasting Help Me Stay Ahead of the Game?
With demand forecasting, you can predict how much of your product you’ll need in the future. By looking at past sales data and current trends, you can adjust your production schedule, manage inventory better, and keep customers happy by never running out of stock—or having too much sitting around.
4. How Can Analytics Improve My Supply Chain and Logistics?
Analytics gives you real-time visibility into your supply chain, from inventory levels to supplier performance. By knowing exactly where everything is, you can make sure materials move smoothly through your operations, avoid delays, and reduce costs—keeping everything efficient and on time.
5. How Does Manufacturing Analytics Help Me Maintain Consistent Quality?
Real-time monitoring means you catch any quality issues before they turn into bigger problems. You can spot defects during production, prevent rework, and keep your products consistent. That means happier customers and less waste.
6. How Can Price Optimization Boost My Bottom Line?
Price optimization lets you adjust your prices based on market demand and production costs. By using data to figure out the best price for your product, you can stay competitive, increase sales, and still protect your profit margins. It’s about finding the sweet spot where price and demand meet.
7. How Can Analytics Improve My Product Development Process?
Analytics gives you deep insights into what your customers really want. By analyzing customer feedback and purchasing patterns, you can design products that hit the mark. Plus, you can speed up development, get products to market faster, and keep customers coming back for more.
8. How Does Automation and Robotization Help My Factory?
Robots and automation are game-changers in manufacturing. By automating repetitive tasks, you reduce errors, speed up production, and free up human workers for more complex tasks. Analytics helps optimize these robots, making them smarter and more efficient, which leads to higher productivity and fewer mistakes.
9. How Does Real-Time Monitoring Improve My Operations?
With real-time monitoring, you get instant alerts on what's happening in your factory. If a machine’s acting up or production is slowing down, you can catch it right away and make fixes before they cause bigger problems. It’s like having a constant pulse on your factory’s health.
10. How Can I Overcome the Challenges of Implementing Analytics?
Introducing manufacturing analytics can be tricky—there’s a lot of data, and you need the right tools and people to make sense of it all. Start by clearly defining what you want to improve. Make sure your tech can handle the data and that your team understands how to use it. With the right setup, analytics will quickly become a powerful tool for smarter decision-making.